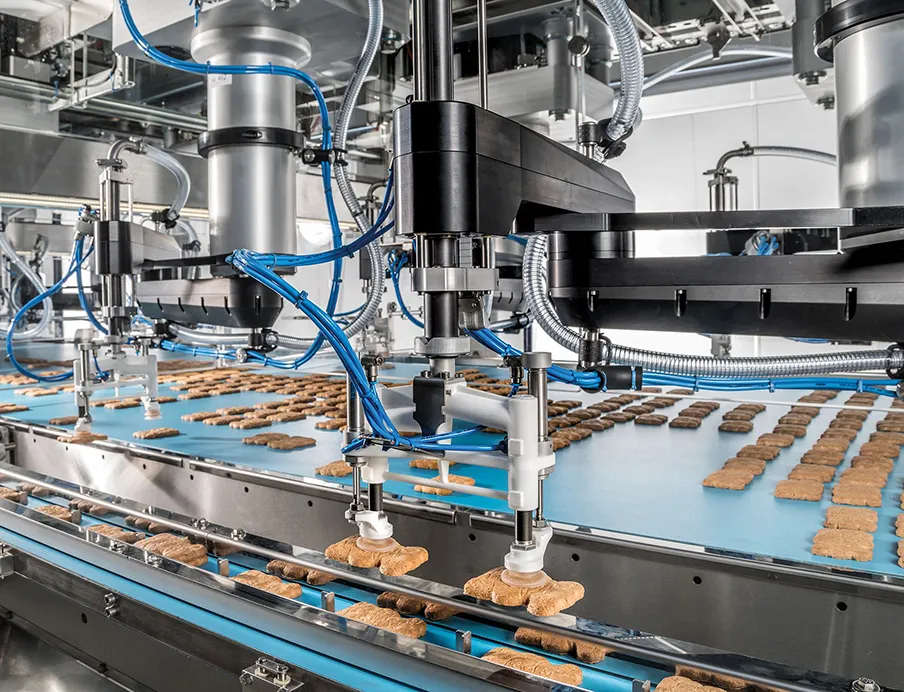
Tradition, family, responsibility, respect - these are the values that the packaging machine manufacturer Schubert stands for, as does the American bakery manufacturer More Than A Bakery, a subsidiary of Richmond Baking. The family-owned company from Versailles, Kentucky, has more than 170 years of baking experience. Every day, a variety of biscuits and crackers come off the production line, for global players as well as for small regional customers. Packaging the fragile products in flowpacks is quite a challenge, as it requires flexibility, speed and care. Until now, the company has been working with flow-wrapping machines that required the biscuits to be fed in manually. That's why CEO Bill Quigg was looking for a new packaging line that could combine these processing requirements in a fully automated system, and he came across Schubert.
Packaging line enables greater efficiency, performance and flexibility
On the one hand, the aim was to free staff from the monotonous work of feeding the machine. On the other hand, production losses in the packaging process were to be significantly reduced. In addition, the manufacturer wanted to be able to increase the line's output in the future in order to utilise the full capacity of the oven. Another wish was to be able to switch from the previously used cold-seal film to a variety of heat-seal films. This will enable the company to offer its customers recyclable flow-wrap packaging made of mono films or paper-based films in the future.
Redundant machine concept significantly reduces waste
Schubert has combined these customer requirements in a redundant machine concept based on the Schubert Flowpacker. Here, the Flowmodul flow-wrapping unit is integrated directly into the line to save space. The products are not fed in the conventional way via conveyor belts, but via pick & place robots. This results in a consistently controlled process. During this process, the fragile products are checked for quality using Schubert image processing. Robots take these baked goods extremely gently from the belt and place them in the chain of the flow-wrapping unit. They are then packaged. A flexible sealing unit ensures the best possible sealing process for the respective flowpack film.
Packaging line handles 1,700 products per minute
For More Than A Bakery, Schubert has built a high-performance modular line with four flow modules and 26 F4 robots from its proven system components. The system is designed in such a way that it can still achieve its full output of more than 1,700 products per minute even if one of the flow-wrapping units fails. This means that all products fresh from the oven can still be packed without any loss of goods.
Stefan Hoffmann, Sales Account Manager at Schubert North America, explains the benefits of the robot-assisted packaging technology: “With this fully automated solution, we are helping our customer achieve much higher production performance and reliability than before, while significantly reducing waste." This not only makes the bakery manufacturer more efficient throughout the entire production process, it also allows the company to benefit from lower costs in the long term while increasing its sustainability.
Prepared for recyclable flowpack films
The system itself consists of two flowpackers arranged in series in a line, each of which is symmetrically mirrored. So there are two flow modules working on each machine part on either side of the product conveyor belt. The baked biscuits enter the machine on the wide product conveyor belt. There they are checked for completeness by the vision system using an incident light scanner. In the front part of the machine, six pick-and-place robots each load the chain of their associated form-fill-seal unit in a double-pick process; in the rear part, there are seven robots per unit. The biscuits are then packed in stacks of two or three in cold-seal film.
Flexible sealing units in the packaging line
The baked goods manufacturer currently uses four formats, but it is possible to use many more. The sealing units in the Flowpacker are so flexible that More Than A Bakery can easily switch from the cold-seal process to the hot-seal process. To make this possible, the Schubert experts have already equipped all flow modules with the flying cross-sealing unit for hot-sealing. During cold sealing, the sealing unit remains fixed. During hot sealing, it moves back and forth along the chain so that the sealing time always remains constant despite speed fluctuations. This allows for hot-seal films, sensitive mono films or paper-based films to be sealed securely and without damage. To do this, only the longitudinal sealing unit needs to be replaced and equipped with an ultrasonic sealing unit.
Stefan Hoffmann explains: “If the trend towards recyclable films continues to grow, and we assume it will, More Than A Bakery is already equipped to meet the requirements of its customers with Schubert’s flexible sealing technology and can switch to more environmentally friendly packaging solutions in the shortest possible time.”
Subsequent performance upgrade already integrated
The required increase in output has already been prepared in the line by additional, as yet empty machine frames. If required, they only need to be equipped with robots and scanners from the modular Schubert system. The packaging speed can then be increased so that the line can even handle the maximum output of the oven of 2,600 products. Even higher output requirements can be achieved with a third Flowpacker.
One of the main reasons for choosing a Schubert machine was the opportunity to work with another family-run company. Schubert was also able to meet the request for an extraordinary colour scheme for the system. Each front of the frames is a different colour. The Quigg family was on hand in person for the factory acceptance test in Crailsheim. Stefan Hoffmann is delighted with the successful project: “We aim to make our customers a little more future-proof with every one of our lines. Together with More Than A Bakery, we have achieved this in every respect.”